Hogyan készítsünk egy gépet, és készítsünk egy cinder blokkot?
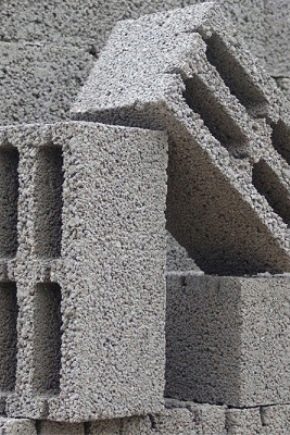
Az építőanyagok köre ma nem örülhet, hanem sokszínűségét illetően, de sokan úgy döntenek, hogy hasonló termékeket készítenek saját kezükkel. Tehát teljesen lehetséges, hogy egy speciális házi készítésű géppel nagy mennyiségű salakköveket készítsünk. Ma részletesen elemezzük, hogyan kell helyesen csinálni.
Anyagi jellemzők
A salakkő olyan építőanyag, amely az egyik legtartósabb és szerényebbnek bizonyult. Jelentős méretekkel rendelkezik, különösen akkor, ha egy szokásos téglát helyez el mellette. A salakblokkok gyártása nem csak gyári beállításban lehetséges. Néhány mester ezt a munkát otthon veszi át. Ha szigorúan betartja a technológiát, kiváló minőségű és erős blokkokat kap, amiből házat vagy melléképületet építhet.
Ha úgy határoznak, hogy önállóan gyártják az ilyen termékeket, akkor számos sajátosságát figyelembe kell venni.
- Salakkő - tűzálló anyag. Nem öngyullad, és nem fokozza a már meglévő lángot.
- Az igazán jó minőségű blokkokból tartós és fenntartható lakások / mezőgazdasági épületek alakulnak ki. Sem az erõs éghajlati viszonyok, sem a hurrikánok, sem az állandó gusty szél nem károsítja az ilyen épületeket.
- A cinder blokk épületek javítása nem igényel felesleges energiát és szabad időt - az összes munka rövid időn belül elvégezhető.
- A salakköveket nagy méretük is megkülönbözteti, melynek köszönhetően az épületek nagyon gyorsan felépülnek, és sok építőt kedvelnek.
- Ezt az anyagot tartósság jellemzi. Az épületből épült épületek több mint 100 éve állhatnak fenn anélkül, hogy elvesztették volna a korábbi jellemzőiket.
- A cinder blokk másik jellemzője a zajszigetelő alkatrész. Tehát az anyagból készült otthonokban nincs idegesítő utcai zaj.
- A salakblokkok előállítását különböző nyersanyagok felhasználásával végezzük, ezért lehetőség van az optimális termékek kiválasztására bármilyen körülmények között.
- A cinder blokkban különbözik, és az a tény, hogy nem kerül különféle paraziták vagy rágcsálók támadásainak. Ezenkívül nem rothad, ezért nem szükséges az antiszeptikus oldatokkal és más, a szubsztrátum védelmére tervezett hasonló vegyületekkel bevonni.
- A tisztességes méretek ellenére az ilyen blokkok kis súlyúak. Ezt a funkciót sok mester látja. Ezeknek az anyagoknak a könnyedsége miatt lehetőleg zökkenőmentesen mozoghat egyik helyről a másikra anélkül, hogy csapot okozna. Meg kell azonban jegyezni, hogy az ilyen termékek néhány fajtája még mindig meglehetősen nehéz.
- A salakkő nem fél az alacsony hőmérsékletektől.
- Ezeket a blokkokat magas hőteljesítményük jellemzi, aminek köszönhetően hangulatos és meleg lakások találhatók tőlük.
- A hőmérséklet-ugrások nem ártanak a cinder blokknak.
- A salak épületeket általában dekoratív anyagokkal díszítik, hogy az esztétikusabb megjelenés legyen. Nagyon fontos azonban megjegyezni, hogy a cinder blokkot nem szabad szokásos vakolattal fedni (az ilyen anyaggal végzett „nedves” munkát nem szabad elvégezni). Használhat egy speciális dekoratív blokkot is, amelyet gyakran drága bélés helyett használnak.
- A cinder blokk használatakor fontos figyelembe venni az egyik fontos jellemzőt - az ilyen anyagot nagy vízfelvétel jellemzi, ezért védeni kell a nedvességgel és nedvességgel való érintkezés ellen. Ellenkező esetben a blokkok idővel összeomolhatnak.
- Sajnos a salakblokkok geometriája sok kívánnivalót hagy maga után. Ezért, az ilyen anyagok átfedésének megállapításával, folyamatosan módosítania kell az egyes elemeket - vágni és látni.
- A salak blokkok viszonylag alacsony költséggel rendelkeznek.
A szakértők szerint a munka ilyen anyagok elég szeszélyes, így mindig nagyon fontos, hogy kövesse a megfelelő utasításokat. Ugyanez vonatkozik a gyártási folyamatra is.
A keverék összetétele
A salakblokkok előállítása otthonban megköveteli, hogy a mester egy adott összetételhez, valamint az összes komponens bizonyos arányához ragaszkodjon. Így a cementet általában ebben az anyagban kötőanyagként használják, és az M400-nál nem alacsonyabb minőségű. Ami a töltő komponenst illeti, az teljesen salakból állhat, vagy keverhető. Az utolsó opciót kis mennyiségű kavics, homok (egyszerű vagy bővített agyag), zúzott tégla és kis frakció claydite hozzáadásával nyerjük.
A cinder blokkok gyártásánál az alábbi arányoknak kell megfelelniük:
- 8-9 rész a töltő komponensből;
- 1,5-2 rész kötőanyag-összetevőt.
Ha a munkamenet során az M500 jelzéssel használták a cementet, akkor 15% -kal kisebb az M400 nyersanyagnál. Az ilyen elem, mint salak, leggyakrabban a töltőanyag teljes térfogatának legalább 65% -át foglalja el.
Például 9 részből nem kevesebb, mint 6 esik erre a komponensre, és a fennmaradó térfogat kavicsra és homokra esik. Elméletileg, saját gyártás során megengedett beton- vagy téglaharc használata, szűrés.
A cinder blokk standard arányai:
- 2 darab homok;
- 2 rész kavics;
- 7 rész salak;
- 2 darab M400 jelzésű portlandcement.
Ami a vizet illeti, a szokásos hozzávetőlegesen 0,5 rész arányban adjuk hozzá. Az eredmény egy félig száraz oldat. A kiváló minőség biztosítása érdekében egy kis maroknyi és kemény felületre kell dobnia. Ha egy elhagyott csomó összeomlott, de tömörítési körülmények között visszanyerte korábbi alakját, akkor a kompozíció további felhasználásra alkalmasnak tekinthető.
Ha színes cinder blokkot kíván kapni, a receptet színes kréta vagy tégla por egészíti ki. Az anyag szilárdsági jellemzőinek javítása érdekében speciális lágyítószereket használjon. Bizonyos esetekben gipsz, hamu vagy fűrészpor hozzáadására vonatkozik.
Javasoljuk, hogy az összes felsorolt alkatrészt egy speciális keverőbe vagy betonkeverőbe keverjük, azonban ezeknek a berendezéseknek általában magas ára van. Ha egy kis mennyiségű keverék előkészítéséről beszélünk, kézzel lehet gyúrni, annak ellenére, hogy egy ilyen folyamat eléggé munkaigényesnek tekinthető.
Formázási módszerek
A fahéjblokkok előállítására szolgáló gyári formák vasbetonból vagy acélból készülnek. Az ilyen részek könnyen megtartják az oldat tömegét nagy térfogatban. Ami az ön által készített formákat illeti, leggyakrabban fából vagy acéllemezből készülnek. Az ilyen elemek nagyobb szerepet játszanak a speciális zsaluzásban.
A nyersanyagok és a szabadidő megtakarításához a formákat főleg az alsó rész nélkül gyűjtöttük össze. Alattuk egy egyszerű filmet. Ennek a módszernek köszönhetően jelentősen leegyszerűsíthető a blokkok kialakításának teljes folyamata. Emlékeztetni kell arra, hogy maguknak a formáknak tökéletesen sima fás részekből kell készülniük. A munkafelület egy beton alap, egy sík és sima asztallap vagy egy vaslemez, amely szintén nem rendelkezik hibával.
Sok mester használ üvegpalackokat üregek létrehozásához. A műanyag tartály nem érdemes megvenni, mivel súlyosan fürdhet. Palackok öntött vizet.Ellenkező esetben lebegnek az előkészített készítmény felületén.
Nézzük meg közelebbről, hogy hogyan készítsünk egy formát a salakblokkokhoz:
- ki kell választani a 14 cm hosszú polírozott lapokat (a szélességnek ennek a paraméternek a többszörösét kell képeznie);
- majd egy fűrészfűrész használatával el kell különíteni a szegmenseket, amelyek ezután a keresztirányú partíciók szerepét fogják játszani;
- akkor a szegmenseket a hosszanti elemekkel kell összekötni a négyszögletes keret létrehozásához;
- aztán meg kell vágni egy acéllemezt vagy más, sima felületű anyagot különálló lemezekre, amelyek mérete 14x30 cm;
- a kapott szerkezet belső részén vágásokat készítenek, amelyek hornyként fognak működni, amelynek szélessége megegyezik az elválasztócsíkok méreteivel;
- ezután a szétválasztásért felelős szegmenseket vágásokkal rögzítettük, és 3 vagy több salakblokk előállítására szolgáló formát hozunk létre.
Annak érdekében, hogy a kapott oldat a lehető legrövidebb időn belül megszilárduljon, a végső szakaszban mind fém-, mind a faszerkezeteket olaj alapon kell festeni. Ez az űrlap 14 mm x 14x30 cm-es mérőhüvelyek készítésére alkalmas.
Ha más dimenziós paraméterekkel rendelkező elemeket kell készíteni, akkor az eredeti értékek más méretekre változnak.
Hogyan készítsünk vibromachint?
A salak blokkokat otthon készítjük egy speciális rezgőgép segítségével, amely kézzel is elkészíthető. Ennek a készüléknek a fő összetevője maga a vibroform az oldathoz. Egy ilyen gép olyan acél doboz, amelyben az üregekkel vagy anélkül rögzített alkatrészek vannak rögzítve. Maga a mátrix már gép. Megengedett, hogy a manuális módon bizonyos szakaszokat végezzen.
A rezgő gép önmagában történő gyártásához meg kell vásárolni:
- hegesztőgép;
- daráló;
- vice;
- szerszám a vízvezetékhez.
Ami az anyagokat illeti, szüksége lesz:
- acéllemez 3 mm - 1 négyzet. m;
- 75-90 mm - 1 m átmérőjű csövek;
- 3 mm-es acélszalag - 0,3 m;
- 500-750 W elektromos motor;
- anyák és csavarok.
Tekintsük a házi vibrobank gyártásának sorrendjét.
- Mérje meg a standard salakblokkot vagy rögzítse a szükséges paramétereket.
- Vágja le a gép oldalsó részeit egy fémlemezből. A cinder blokkok száma alapján adja meg a szükséges partíciók számát. Ennek eredményeképpen 2 (vagy több) azonos rekeszből egy doboz van kialakítva.
- Az alsó falnak legalább 30 mm vastagságúnak kell lennie. E paraméter alapján meghatározzuk a henger magasságát, korlátozva az üregeket.
- Vágjunk 6 egyedi csőhosszra, amelyek megfelelnek a henger magasságának.
- Ahhoz, hogy a hengerek kúp alakú szerkezetet szerezzenek, megengedhetjük, hogy hosszirányban vágjuk őket a középső részre, összenyomjuk a szerszámmal, majd hegesztéssel csatlakozzanak. Ebben az esetben az elemek átmérője 2-3 mm-rel csökken.
- A hengereknek mindkét oldalon kell főzniük.
- Ezenkívül ezeket az alkatrészeket egy sor formájában kell egymással összekötni, a jövő cinder blokk hosszú oldalának mentén. Meg kell ismételniük az üregek helyét a gyári elemben. A széleinél 30 mm-es lemezt kell rögzíteni, amely lyukakkal van ellátva a szemekhez.
- A mátrix minden egyes rekeszének közepén propil- és hegesztett szemet kell készíteni. Ez azért szükséges, hogy biztosítsa az ideiglenes rögzítőelemek korlátozását az üregek ürítéseire.
- A külső keresztirányú falhegesztésnél 4 csavar van a motor szerelőnyílása alatt.
- Ezután húzzuk meg a kötényt és a lapátokat az élek mentén azon a helyen, ahol a rakodást végzik.
- Ezután folytathatja a festés minden elemének elkészítését.
- Készíthet egy sajtót, amely megismétli a mechanizmus alakját egy olyan lemezen, amelynek lyukai 3-5 mm-rel nagyobbak, mint maguk a hengerek. A lemez zökkenőmentesen lépjen be a dobozba 50-70 mm mélységbe, ahol korlátozó részek vannak.
- Meg kell hegeszteni a fogantyúkat a sajtóhoz.
- Most a berendezés elfogadható a vibrációs motor festésére és rögzítésére.
Termelési technológia
A salakblokkok kétféleképpen készülnek.
- Könnyű út. Ebben az esetben speciális tartályokat használnak, amelyekben az elkészített oldat megszerzi a szükséges szilárdságot. Természetesen megszárad, amíg a cement teljesen megszilárdul.
- Nehéz út. Ezzel a módszerrel a használt rezgőberendezések gyárthatók. Sok esetben olyan elemeket kezelnek, mint a rezgő asztal, vagy kiegészítik az űrlapot egy rezgés funkcióval ellátott motorral.
Ismerje meg a salakblokkok gyártási technológiáját egyszerű formák segítségével.
- Minden előkészített összetevőt a kívánt arányban betonkeverőbe helyezünk, majd alaposan összekeverjük.
- A kész oldatot öntőformákba öntjük. Ami a tampingot illeti, azt kalapáccsal végzik el - a tartályt kopogtatják úgy, hogy az egész levegő elhagyja az anyagot.
- Ha a tömböket üregekkel tervezik megtenni, akkor az egyes részekbe vizes palackok kerülnek (általában 2 palack elegendő).
Ennek a gyártási módszernek a fő problémája a tampingblokkok. Ha a légbuborékok az oldat belsejében maradnak, ez hátrányosan befolyásolja a végtermék minőségét.
Ami a salakblokkok előállításának összetettebb módját illeti, itt a következő munkát végezzük:
- Az ilyen anyagok előállításának megkezdésével a keveréket a keverőben kell keverni;
- a kapott oldatot az öntőformába továbbítjuk, majd simítóval simítjuk;
- ezután elindul a vibrátor, és maga a megoldás 20-60 másodpercig marad formában;
- majd a berendezést ki kell kapcsolni, a telepítést fel kell emelni, majd a kész egységet el kell távolítani.
A technológia alkalmazásával a salakblokkok gyártásakor különös figyelmet kell fordítani a habarcs szintezésére a sarokrészekben. Meg kell tölteni őket. Ellenkező esetben a késztermék geometriája súlyos hatással lehet.
szárítás
A szárítás egy másik fontos lépés a salak blokkok gyártásában. A termelési folyamat általában 2-4 napig tart. 28 nap elteltével általában elegendő szilárdsági jellemzők érhetők el, amelyek lehetővé teszik a blokkok használatára való áttérést. Ez az az idő, amely szükséges ahhoz, hogy bizonyos munkák elvégzéséhez alkalmas, kiváló minőségű építőanyagot kapjunk. A cinder blokkok természetesen kiszáradhatnak. Általában ez a folyamat az anyagok egyszerű gyártási módszerével történik (hagyományos formában).
Szárításkor a cinder blokkok gyakran speciális kamrákat használnak, amelyek megakadályozzák a repedést keményedésük során. Annak érdekében, hogy a tömbök ne repedjenek, időről időre meg kell nedvesíteni őket. Ez a folyamat különösen fontos, ha a termelési folyamatot meleg időben végzik.
Meg kell jegyezni, hogy a cinder blokkok keményedése jelentősen felgyorsítható. Ez a hatás speciális anyagok hozzáadásával érhető el - lágyítók. Ilyen adalékanyagok esetén az anyag nem csak gyorsabban kiszárad, hanem erősebb is lesz. A lágyítószereket tartalmazó salakblokkok eltávolíthatók a helyszínről és 6-8 óra elteltével tárolhatók.
Tippek és trükkök
- A cinder blokk elülső oldalán pontosabbnak és teljesebbnek bizonyult, ezeket a szárítóanyagokat lapos gumi alapra kell helyezni.
- A szárítás során soha ne tegye egymás tetejére a tömböket. Ellenkező esetben az anyagok deformálódhatnak, és geometriájuk sok problémát okoz az építés során.
- Minden esetben először rajzokat kell készítenie a formákról és a salakblokkokról. Így az építési folyamatokkal kapcsolatos számos nehézség elkerülhető.
- Az oldat elkészítésekor ügyeljen arra, hogy a szükséges arányokat betartsa.A legkisebb hibák azt eredményezhetik, hogy a blokkok túl törékenyek és nem alkalmasak az építésre.
- Az elkészített oldat öntése előtt a formákat meg kell törölni. Tehát megakadályozza, hogy a cinder blokkok az aljára és a falakra tapadjanak. A tisztításhoz leggyakrabban dízelolajat, hulladékolajat vagy más hasonló anyagot használnak.
- Megjegyezzük, hogy az oldat megszilárdulási sebessége közvetlenül függ a vastagságától. Minél vastagabb a kompozíció, annál gyorsabbak lesznek a blokkok.
- A szárítás időtartama alatt a salak blokkot polietilénnel kell bevonni. A film képes lesz arra, hogy megvédje az anyagot a forró időjárásban fellépő repedések megjelenésétől, valamint megvédje a csapadék blokk nedvesedését, ha esik.
- Ha kis mennyiséget akar megtakarítani a salakalkatrészek gyártásában, akkor 3 és 1 mész és cement arányban lehet kombinálni. Nem kell aggódnia a cinder blokkok minősége miatt - az ilyen összetételből nem lesz kevésbé megbízható.
Hogyan készítsünk salakblokkoló gépet 4 blokkhoz, lásd az alábbi videót.